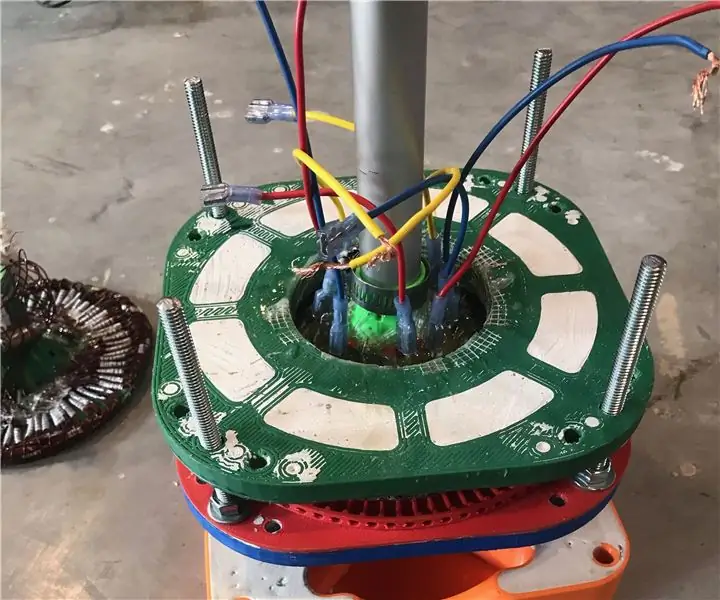
Tartalomjegyzék:
2025 Szerző: John Day | [email protected]. Utoljára módosítva: 2025-06-01 06:09
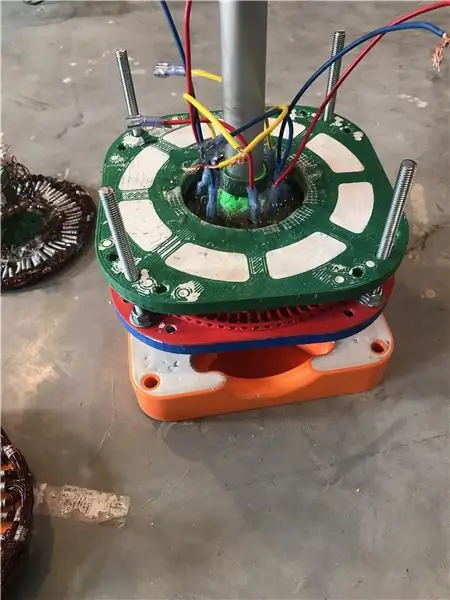
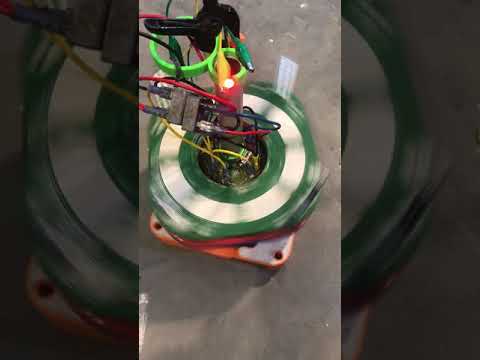
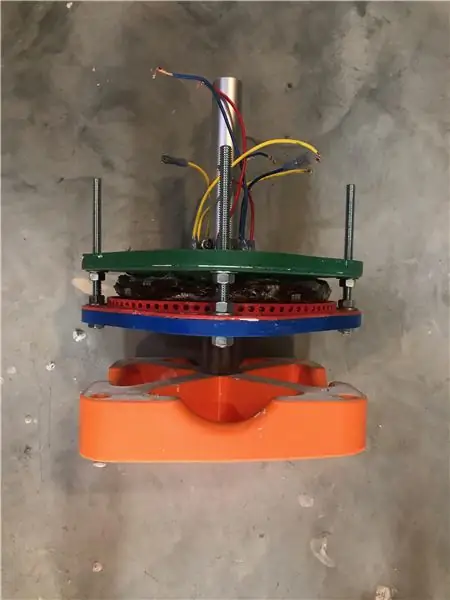
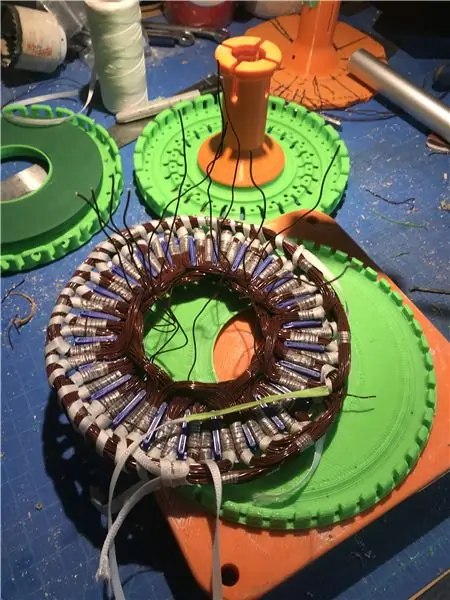
ÁLLJON MEG!! ELŐTT OLVASSA EL !!! Ez egy folyamatban lévő projekt rekordja, kérjük, bátran támogasson.
A végső célom az, hogy ez a fajta motor/generátor parametrizált nyílt forráskódú kialakítássá váljon. A felhasználónak képesnek kell lennie bizonyos paraméterek megadására, mint például a nyomaték, a sebesség, az áram, a volt/ford/perc, a közös mágnesméretek és talán a rendelkezésre álló hely, valamint egy sor 3D nyomtatható.stl és.dxf kivágott fájlt kell létrehozni.
Amit tettem, egy olyan platformot hoztam létre, amely képes validálni egy szimulált tervezést, amelyet aztán a közösség optimálisabb eszközzé fejleszthet.
Részben ez az egyik oka annak, hogy ezt dinamométerrel állítottam be. A dinamométer méri a nyomatékot és a fordulatszámot, hogy lehetővé tegye a LE vagy a tengely wattjának mérését. Ebben az esetben a generátort átmenő, álló tengelyűre építettem, ami egyszerűbbé teszi a dinamométer rendszer felállítását, és így konfigurálható úgy, hogy RC ESC motorként vezesse (remélem), és mérje meg a nyomatékot a kimeneten, valamint a fordulatszám, V és erősítők, lehetővé téve a motor hatékonyságának meghatározását.
Céljaim szerint változtatható fordulatszámú motorral hajtható (az akkumulátoros fúróból származó többlet, csökkentett hajtóművel), és mérhető a tengelynyomaték bemenete, valamint V és Amper kimenet, lehetővé téve a valódi hatékonyságot és a várható turbina terhelést szimulálni kell.
Ebben a módban remélem, hogy RC ESC -t használok, amely képes a regeneratív fékezésre, és talán egy Arduino -t, hogy ellenőrizzék a terhelést, amelyet a VAWT hordoz az MPPT (Multi Power Point Tracking) elérése érdekében.
Az MPPT -t a napenergia és a szélturbina vezérlésében használják, de a szélnél ez egy kicsit más. A szélerőműveknél nagy probléma, hogy mivel a szélsebesség megduplázódik 10 km/h -ról 20 km/h -ra, a szélből elérhető energia a kockával növekszik, tehát 8 -szorosára. Ha a 10W 10 km/h sebességgel elérhető, akkor a 80 W 20 km/h sebességgel érhető el. Nagyszerű, hogy több energiánk van, de a generátorok teljesítménye csak kétszeresére nő, miközben a sebesség megduplázódik. Tehát ha a tökéletes generátorral rendelkezik a 20 km/órás szélhez, akkor a terhelése olyan erős lehet, hogy 10 km/h sebességnél még be sem indul.
Az MPPT nagy teherbírású szilárdtestalapú kapcsolót használ, hogy nagyon gyorsan lekapcsolja, majd újra csatlakoztassa a generátort. Lehetővé teszi a generátor terhelésének beállítását, az MPPT Multi pedig azt jelenti, hogy különböző terheléseket állíthat be különböző sebességekhez.
Ez nagyon hasznos, mivel minden típusú turbina összegyűjti maximális energiáját, amikor a terhelést a rendelkezésre álló energiához vagy a szélsebességhez igazítják.
ÍGY
Ez nem recept, bár úgy gondolom, hogy le lehet másolni az általam közzétett tartalomból, és szívesen adok további információkat, de azt javaslom, hogy a legjobb megoldás az lenne, ha javításokat javasolna nekem az áramkörök és érzékelők verseny befejezése előtt, hogy megfontolhassam, reagálhassak és talán javíthassam ezt az oktathatót.
Folytatni fogom az információk frissítését, felülvizsgálatát és hozzáadását, így ha ez most érdekes, érdemes egy idő múlva újra bejelentkeznie, de remélem, hogy a Július 29/19 -én lezajló Érzékelők vetélkedő előtt jó sokat eljutok.
Ezenkívül nem vagyok különösebben társasági állat, de szeretek néha-néha megveregetni a hátát, és ez az egyik oka annak, hogy itt vagyok. többet kérlek:-)
Ez a projekt azért jött létre, mert szabályozható terhelést akartam a turbina terveim tesztelésére, és azt akartam, hogy könnyen reprodukálható legyen, hogy mások is használhassák. Ebből a célból kényszerítettem magam arra, hogy olyasmit tervezzek, amelyet csak FDM nyomtatóval lehet megépíteni, nincs szükség más szerszámgépekre. Úgy tűnik, nincs sok kereskedelmi termék, amely kielégíti a nagy forgatónyomatékú, alacsony fordulatszámú, meg nem kúszó generátor igényét, bár vannak olyanok Kínából. Általánosságban elmondható, hogy nincs nagy kereslet, mert a hajtóműrendszerek annyira olcsók, és az áram annyira olcsó.
Amit akartam, valami olyan volt, amely 12 V körül 40-120 fordulat / perc, és 600-750 W körül 120-200 fordulat / perc körül termelődött. Azt is szerettem volna, hogy kompatibilis legyen az RC világ olcsó 3 fázisú PMA vezérlőivel (az ESC elektronikus sebességszabályozóival). A végső követelmény az volt, hogy kifutó legyen (a mágneses tok vagy burkolat forog, míg az állórész tengely álló), egy tengely, amely végighalad a házon, és egy állórész, amely a tengelyhez szorul.
Ez az oktatható folyamatban lévő munka, és azért teszem közzé, hogy az emberek rálátást kapjanak a folyamatra, nem annyira, mert szerintem másolniuk kell. A legfontosabb dolog, amin változtatni szeretnék, az az, hogy az általam épített huzaltámasztó lemez közel sem elég erős ahhoz, hogy megfelelően irányítsa a mágneses mezőket a gyűrű körül, így a mágnesekben fizetett mágneses fluxus nagy része kárba vész. Amikor újratervezem a tervezést, amit hamarosan meg is fogok tenni, valószínűleg a mágneses hátlapokat csinálnám, mint cnc vágott acéllemezeket. Az acél meglehetősen olcsó, sokkal erősebb lenne, és egyszerűsítené az építés nagy részét. Érdekes volt olyan FDM/huzal/gipsz kompozitokat csinálni, mint amit itt illusztráltam, és vasbetöltött PLA -val a dolgok is másképp lettek volna. Úgy döntöttem azonban, hogy szeretnék valamit, ami valóban tartós, tehát acéllemezeket.
Jól haladtam ezzel a verzióval kapcsolatban, amelyet a VAWT tesztelésére fogok használni. Az alacsony feszültségű teljesítmény tekintetében még nem vagyok ott. Azt hiszem, a teljesítményem/nyomatékom a megfelelő labdajátékban van, a dolgok előrehaladtával frissítem, de ezen a ponton jó esélyem van arra, hogy a szükséges szabályozható terhelés legyen. Amikor holtzárlatos, úgy tűnik, hogy képes egy kis nyomaték -ellenállást biztosítani, ami több mint elegendő a turbina teszteléséhez. Csak egy ellenőrzött ellenállási bankot kell létrehoznom, és van egy barátom, aki segít nekem ebben.
Egy dologgal röviden foglalkozom, mint sok emberhez hasonlóan, nekem is van néhány éve 3D (FDM-használó PLA) nyomtatóm, amiből 20-30 kg-os élvezetem volt. Gyakran elkeserítőnek találom, bár bármilyen méretű/erősségű alkatrész drága és nagyon lassan nyomtatható, vagy olcsó, gyors és gyenge.
Tudom, hogy hány ezer ilyen 3D nyomtató van kint, gyakran nem csinál semmit, mert sokáig tart, vagy túl sokba kerül a hasznos alkatrészek elkészítése. Érdekes megoldást találtam ki az erősebb, gyorsabb alkatrészekre ugyanazon a nyomtatón és a PLA -n.
Ezt "öntött szerkezetnek" nevezem, ahol a nyomtatott tárgy (1 vagy több nyomtatott részből, néha csapágyakból és tengelyekből áll) olyan üregekkel készül, amelyeket keményedő folyékony töltőanyaggal kell önteni. Természetesen az öntött töltelék nyilvánvaló választási lehetőségei közé tartozik a rövid szálú aprított üvegszállal töltött epoxi, amely nagy szilárdságú és könnyű szerelvényekhez használható. Kipróbálok néhány alacsonyabb költségű, környezetbarátabb ötletet is. Ennek az "öntött szerkezetű" szerelvénynek a másik oldala az, hogy az üreg vagy üreg, amelyet kitölteni fog, kis átmérőjű, nagy szakítószilárdságú elemekkel rendelkezhet, amelyeket a nyomtatott "öntőforma/dugó" -ra előfeszítenek, ami a kapott szerkezetet eredményezi anyagból és szerkezetből álló kompozit, részben stresszes bőr (a PLA burkolat), de nagy nyomószilárdságú maggal, amely nagy szakítószilárdságú elemeket is tartalmaz. Csinálok egy második tanulságos dolgot, amely bemutatja ezt, ezért itt fogok beszélni róla, csak hogy kitérjek arra, hogy ez hogyan kapcsolódik ehhez az összeállításhoz.
1. lépés: Anyaglista és folyamat
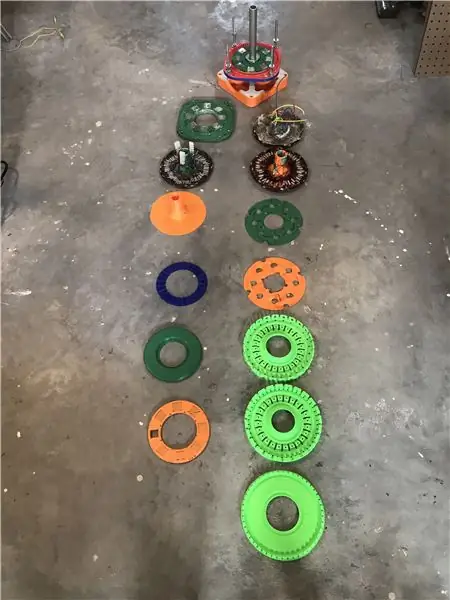
A PMA 3 szerelvényből áll, amelyek mindegyike különböző alkatrészeket és anyagokat tartalmaz vagy használ.
Fentről (csapágyoldal) lefelé (állórész oldal), 1. Csapágytartó és felső csapágytömb
2. Állórész
3. Alsó mágnes tömb
1. A csapágyhordozó és a felső mágnes tömb
Ehhez a fent felsorolt 3D nyomtatott alkatrészeket használtam
- 150mm8pólusú felső mag és csapágytartó CV5.stl,
- csapágy oldali belső lemez
- csapágy oldali külső lemez
- 1 "azonosító önbeálló csapágy (mint a szokásos párna blokkoknál használt ++ internetes link hozzáadása),
- 25 '24 g horganyzott acélhuzal
- 15 '10 g horganyzott acélhuzal
- 2 tekercs durva acélgyapot
Opcionálisan a nehéz acélhuzalt és az acélgyapotot le lehet cserélni acél hátlapokra, lézer / vízsugaras vágásra, vagy lehetséges 3D nyomtatott mágneses hátlap (de a nehéz acélhuzal még mindig jó ötlet, mivel ellenáll a műanyag deformációnak) idő). Próbáltam önteni egy alátétlemezt vas -oxid porral töltött epoxiddal, és némi sikerrel jártam. Ha a tömb mágnesei közötti fluxuscsatlakozást oldalirányban javítják egy hatékonyabb alátétlemez használatával, növelni kell a feszültséget alacsonyabb fordulatszámon. Azt is érdemes szem előtt tartani, hogy ez a fő szerkezeti elem, és a hátlap továbbítja az erőt a mágnesekről az emelőoszlopokra. A lemezeket egymás felé húzó mágneses erők több száz fontot tehetnek ki, és az erők exponenciálisan növekednek (kockázva, a harmadik erőig), amikor a lemezek közel kerülnek egymáshoz. Ez nagyon veszélyes lehet, és körültekintően kell eljárni a szerszámokkal és minden más olyan tárggyal, amelyek vonzódhatnak az összeszerelt lemezhez vagy vissza!
Körülbelül 300 láb 24 g bevont mágneshuzalt használtam a tekercsekben, amelyeket később részletesen lefedek.
2. lépés: A mágneslemezek gyártása
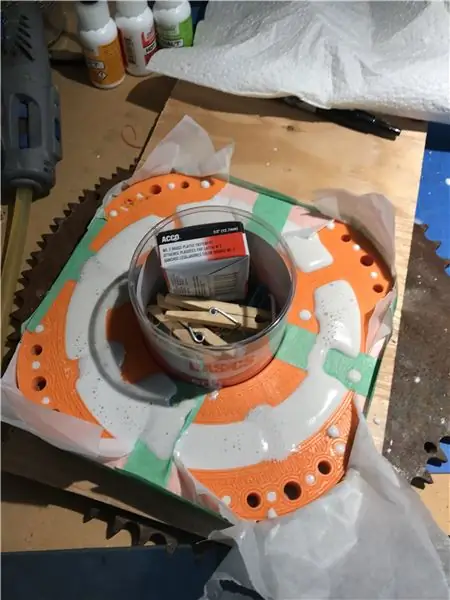
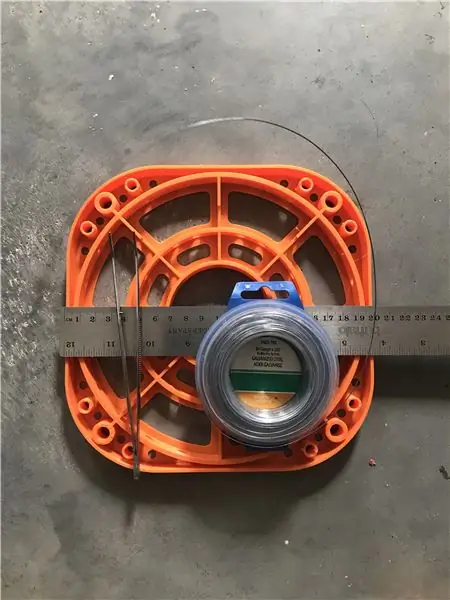
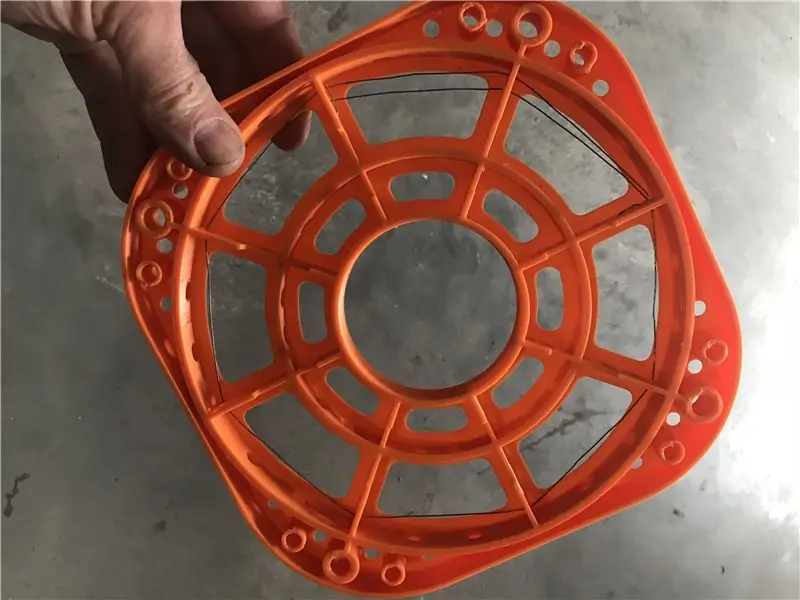
Ebben az axiális fluxusú generátorban, az eltömődés minimalizálása és a kimenet maximalizálása érdekében két mágneses tömböt használok, egyet az állórésztekercsek mindkét oldalán. Ez azt jelenti, hogy nincs szükség mágneses magra, hogy a mágneses mezőt a réz tekercseken keresztül húzza, mint a legtöbb motor/alt geometria. Vannak olyan tengelyirányú fluxusok, amelyek ferris magokat használnak, és a jövőben megpróbálhatok néhány kísérletet. Szeretnék kipróbálni egy 3D nyomtatható vasalható anyagot.
Ebben az esetben egy 8 pólusú mágnes tömböt választottam körülbelül 150 mm körben, 1 "x1" x0,25 "ritkaföldfém mágneseket használva. Ez a méret biztosította, hogy minden alkatrész elférjen egy 210 x 210 mm -es nyomtatóágyon. Általában először úgy méreteztem ezt a generátort, hogy megértettem, hogy minél nagyobb az átmérő, annál jobb a fordulatszám / perc volt, ezért akkora lett, mint amennyi kényelmesen elfér a nyomtatóágyamban. mágnesek, minél távolabb vannak a mágnesek a középponttól, annál gyorsabban haladnak, és több hely jut a réznek is! Mindezek gyorsan összeadódhatnak! Azonban arra a következtetésre jutottam, hogy ebben a mérettartományban egy hagyományos A fluxusrendszer jobb otthoni felépítés lehet. A kis rotoroknak nincs sok helyük, és a dolgok meglehetősen szűkösek lehetnek, különösen akkor, ha átmenő tengelyt csinálnak, mint én ebben a kialakításban. Ha a mágnes (radiális hossz) kicsi a rotor átmérőjéhez képest, mint ebben (nagyjából 6 "átmérőjű 1" mágnes), akkor a windi ng kissé furcsa lesz, mivel a belső végtekercs csak körülbelül 1/2 a külső hosszának.
Vissza az oktatáshoz! Ennek a generátornak a mágneslemezeit úgy szereltem össze, hogy először ragasztom a mágneslemezt (zöld) a piros karimához/hátlaphoz. Ezt követően a mágneslemezt néhány vékony réteg rétegelt lemezre (kb. a mágneslemezek hátulján. Ez nem egészen úgy történt, ahogy reméltem. Az erős mágneses mező a huzalt a mágnesek középpontja felé húzta, és nem sikerült minden sort meghajlítanom, hogy tökéletesen illeszkedjen a következő helyre, anélkül, hogy meglökte volna az első csomagolást. Reméltem, hogy csak be tudom csavarni a vezetéket, és a mágneses fluxus lezárja. Ezután megpróbáltam vágni a huzalgyűrűket, és ez jobb volt, de még mindig messze attól, amit reméltem, hogy szép konzisztens alátámasztólemezt kapunk a huzalból. Ennek megvalósítása bonyolultabb módon lehetséges, és érdemes lehet kísérletezni a jövőben. Megpróbáltam a mágneses mezőben tömörített acélgyapotot is használni alátétlemezként vagy fluxusként Ez látszólag működött, de a tényleges vassűrűség nem tűnt túl magasnak, ezért di Ne tesztelje a hatékonyságát, részben azért, mert úgy gondoltam, hogy a huzal szerkezete fontos a mágneslemezek mechanikai terhelése szempontjából. Az acélgyapot is érdemes lehet a jövőbeni vizsgálatra, azonban a vízsugaras vágású acéllemezek valószínűleg a következő lehetőség, amit megpróbálok.
Ezután vettem a narancssárga 3D nyomtatott részt, és sodortam rajta drótot, körülötte, úgy tűnt, hogy a legnagyobb terhelés iránya, csavarról csavarra, és csavarról középre néhányszor minden sarkon. A csavarfuratok köré is feltekerem, ahol az összes menetes rúd emelőoszlopként halad, hogy megtartsák és beállíthassák a lemezek közötti távolságot.
Miután megbizonyosodtam arról, hogy a mágneslemez és a karima elég jó, és a narancssárga hátlap kielégítően menetes volt erősítőhuzallal, ragasztóval kötöttem össze a kettőt. Óvatosan kell eljárni, mivel ennek a ragasztócsuklónak vízállónak kell lennie, vagy zárnia kell. Az első két alkalommal szivárgásom volt, és ez rendetlenség, sok vakolatot pazarol, és több stresszt okoz, mint amennyire szüksége van. Azt javaslom, hogy tartson körül kék tapadást vagy más rágógumit, például nem tartós ragasztót, hogy gyorsan megszüntesse a szivárgást. Ha az alkatrészek össze vannak kötve, töltse fel a kívánt megerősítő anyaggal. Kemény vakolatot használtam, PVA ragasztóval módosítva. A vakolatnak el kell érnie a 10 000 psi nyomást, de nem túl feszes (tehát a huzal). Szeretném kipróbálni az epoxit apróra vágott üveggel és cabosil -lal, vagy betonnal és adalékokkal.
Egy praktikus dolog a vakolatban az, hogy ha egyszer rúg, akkor elég sok ideje van, ahol nehéz, de törékeny, és a szivárgások vagy foltok könnyen lekaparhatók vagy leüthetők.
Ebben a kialakításban két mágneslemez található. Az egyiknek csapágya van, egy szabványos 1 -es párnablokk önbeálló egység. Korán benyomtam az enyémet a mágnes tömbbe. Az általam tervezett alkalmazáshoz egy második csapágy található a generátor feletti turbinában, így csak az egy önbeálló csapágyat használta. Ez némi fájdalmat okozott a végén. Ezeket az alkatrészeket úgy is össze lehet szerelni, hogy minden egyes mágneslemez csapágyazott, ha az állórész kimeneti vezetékeit belülről vezetik a szerelt tengelyen keresztül. Ez lehetővé teszi az ellentétesen forgó légcsavarok felszerelését egy közös, nem forgó tengelyre/csőre.
3. lépés: A statátor létrehozása

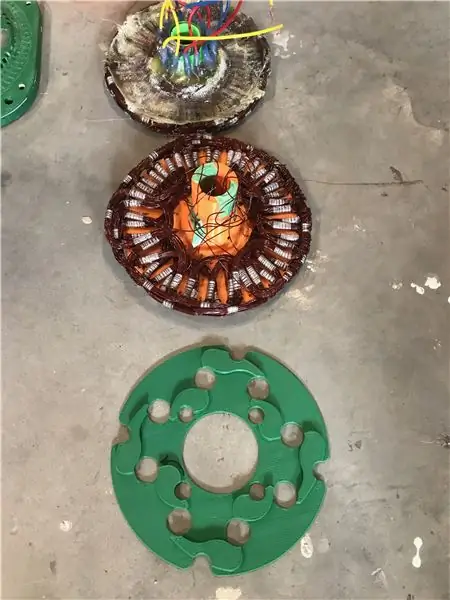
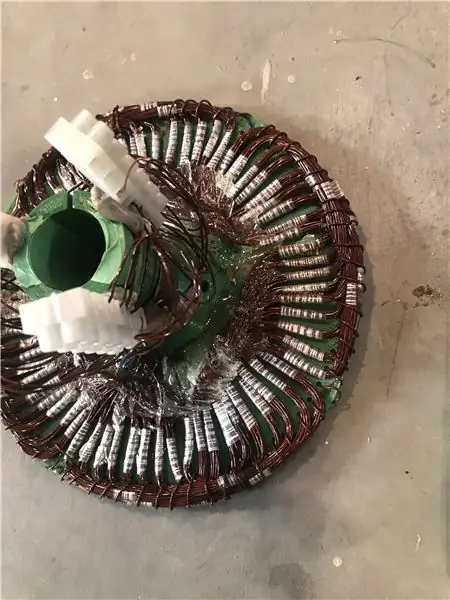
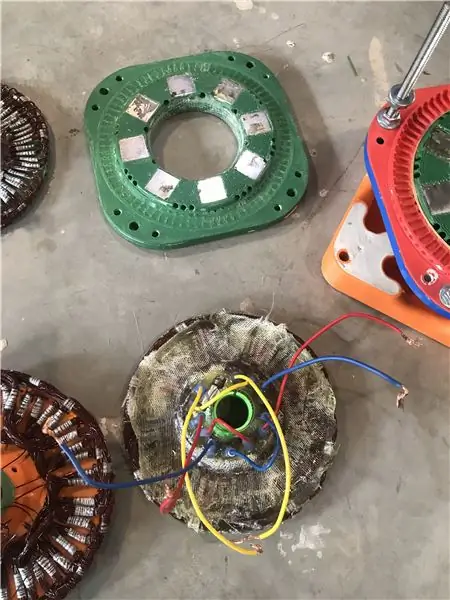
A témámnak megfelelően, hogy megpróbálom elmagyarázni, hogy mit tettem, és miért tűnt akkor jó ötletnek, az állórész egy kicsit több helyet igényel.
A PMA -ban általában a tekercsek álló helyzetben vannak, míg a mágneses szerelvények forognak. Ez nem mindig van így, de szinte mindig. Egy axiális fluxus szerelvényben, az alapvető "jobbkezes szabály" megértésével, minden olyan vezető, amely forgó mágneses mezővel találkozik, áramot és feszültséget generál a huzal végei között, és a hasznos áram mennyisége arányos a mező irányába. Ha a mező párhuzamosan mozog a vezetékkel (pl. A forgástengely körüli körben), akkor nem keletkezik hasznos áram, hanem jelentős örvényáramok keletkeznek, ellenállva a mágnesek mozgásának. Ha a vezeték merőlegesen fut, akkor a legnagyobb feszültség és áramkimenet érhető el.
Egy másik általánosítás szerint az állórészen belüli teret, amelyen forgás közben a mágneses fluxus áthalad, a maximális teljesítmény elérése érdekében a lehető legtöbb sugárirányban lefektetett rézzel kell kitölteni. Ez problémát jelent a kis átmérőjű axiális fluxusú rendszereknél, mivel ebben az esetben a réz számára rendelkezésre álló terület a tengely közelében a külső szélén lévő terület töredéke. Lehetséges, hogy a mágneses tér legbelső részén 100% -ban rezet kapunk, de ezen a geometrián belül csak 50% -ot kapunk a külső szélén. Ez az egyik legerősebb ok, amiért távol kell tartani a túl kicsi axiális fluxustól.
Amint azt korábban már említettem, ez az oktatható nem arról szól, hogyan csinálnám újra, hanem inkább arra, hogy mutasson néhány ígéretesnek tűnő irányba, és mutassa meg az ezen az úton elérhető kátyúkat.
Az állórész tervezésekor a lehető legrugalmasabbá akartam tenni a fordulatszám per perc fordulatszámát, és azt akartam, hogy 3 fázisú legyen. A maximális hatékonyság érdekében a keletkező örvényáramok minimalizálása révén minden "láb" (a tekercs mindkét oldalát "lábnak" kell tekinteni) egyszerre csak egy mágnessel találkozhat. Ha a mágnesek közel vannak egymáshoz, vagy összeérnek, mint sok nagy teljesítményű rc motor esetében, akkor a "láb" áthaladása közben a mágneses fluxus megfordításában jelentős örvényáramok alakulnak ki. Motoros alkalmazásokban ez nem számít annyira, mivel a tekercset a vezérlő táplálja, amikor a megfelelő helyen van.
Ezeket a fogalmakat szem előtt tartva méreteztem a mágnes tömböt. A tömb nyolc mágnese egyenként 1 "átmérőjű, a köztük lévő tér pedig 1/2". Ez azt jelenti, hogy a mágneses szegmens 1,5 "hosszú, és 3 x 1/2" lábnak van helye. Mindegyik "láb" egy fázis, így bármelyik ponton az egyik láb semleges, míg a másik kettő a növekvő és a csökkenő fluxust látja. Tökéletes háromfázisú kimenet, bár a semleges pontnak ennyi helyet adva (az örvényáramok minimalizálása érdekében), és négyzet alakú (vagy pite alakú) mágnesek használatával a fluxus majdnem korán eléri a csúcsot, magas marad, majd gyorsan leesik a nullára. Az ilyen típusú kimenetet szerintem trapéz alakúnak nevezik, és nehéz lehet néhány vezérlő számára, amelyeket megértek. 1 "-os kerek mágnesek ugyanabban a készülékben több valódi szinuszhullámot adnának.
Általában ezeket az otthoni generátorokat "tekercsek", fánk alakú huzalkötegek felhasználásával építették, ahol a fánk mindkét oldala "láb", és számos tekercset lehet egymáshoz, sorba vagy párhuzamosan rögzíteni. A fánkok körbe vannak rendezve, középpontjuk a mágnesút középpontjához igazodik. Ez működik, de vannak problémák. Az egyik probléma az, hogy mivel a vezetők nem sugárirányúak, a vezető nagy része nem halad át 90 fokban a mágneses mezőhöz, ezért örvényáramok keletkeznek, amelyek hőként jelennek meg a tekercsben, és ellenállnak a forgásnak a mágnes tömbben.. Más kérdés, hogy mivel a vezetők nem sugárirányúak, nem pakolnak össze olyan szépen. A kimenet egyenesen arányos az ebben a térben elhelyezett huzalmennyiséggel, így a kimenetet nem sugárirányú "lábak" csökkentik. Bár lehetséges és néha kereskedelmi kivitelezésben is megvalósul, a tekercs felfelé és alul összekapcsolt sugárirányú "lábakkal történő feltekerése kétszer annyi végtekercset igényel, mint egy kígyózó tekercselés, ahol az egyik láb teteje össze van kötve a felsővel a következő megfelelő láb, majd a láb alja csatlakozik a következő megfelelő lábhoz, és tovább.
A másik nagy tényező az ilyen típusú axiális fluxus generátorokban (forgó mágnesek az állórész felett és alatt) a lemezek közötti rés. Ez egy kockajogi összefüggés, mivel a lemezek közötti távolságot 1/2 csökkenti, a mágneses fluxussűrűség 8 -szorosára nő. Minél vékonyabbá teheti az állórészét, annál jobb!
Ezt szem előtt tartva készítettem egy 4 karéjos tekercselőt, beállítottam egy rendszert körülbelül 50 láb huzalszál mérésére, és 6 -szor becsomagoltam a szálat, körülbelül 6 mm átmérőjű huzalkötegeket hozva létre. Ezeket a kék távtartó gyűrűre illesztem, lekötöm őket a lyukakon keresztül, így a huzalvégek a hátsó részből kerültek ki. Ez nem volt könnyű. Segített egy kicsit az, hogy gondosan felragasztottam a kötegeket, hogy ne legyenek lazák, és hogy időt szántam rá, és egy sima faalakító eszközzel nyomtam a vezetékeket a helyükre. Miután mind a helyükre voltak kötve, a kék távolságtartó gyűrűt a világoszöld formázó kádak közül a legnagyobbba helyezték, és a sötétzöld fánkformázó szerszám segítségével a világoszöld kád másik oldalán óvatosan laposra nyomták. padi satu. Ez a formázó kád horonnyal rendelkezik a kötőhuzal csavarásaihoz. Ehhez idő és türelem szükséges, miközben óvatosan elforgatja az 1/5 fordulatot, nyomja, forgatja és folytatja. Ezáltal a korong lapos és vékony lesz, miközben lehetővé teszi a végtekercsek felhalmozódását. Észreveheti, hogy a 4 karéjos tekercsemnek egyenes "lábai" vannak, de a belső és a külső csatlakozások nem kerekek. Ennek az volt a célja, hogy megkönnyítse számukra a halmozást. Ez nem sikerült olyan jól. Ha újra megtenném, a belső és külső végtekercseket körkörös utakon követném.
Miután lapos és vékony lett, és a szélei összepakoltak, lapos szalagot tekertem a szélére, hogy tömörítsem, és egy másikat felfelé, lefelé és minden láb körül, majd a mellette lévőre is. Miután ez megtörtént, távolítsa el a kötőhuzalokat, és váltson a kisebb préselő kádra, majd menjen vissza a satuba, és nyomja meg a lehető legvékonyabban és laposabban. Ha lapos, akkor vegye ki a présfürdőből. Ahelyett, hogy az ilyen formákat óvatosan gyantáznánk és bevonnánk az oldószerekkel, általában csak pár réteg nyújtófóliát használok (a konyhából). Helyezzen pár réteget a forma aljára, és tegye rá az üvegszálat a nyújtható csomagolásra. Ezután tegye hozzá az állórész rögzítőcsövét, amely illeszkedik a világoszöld formázó kád tetejéhez, de van közöttük rugalmas fólia és üvegszál réteg. Ezután tegye vissza az állórésztekercset a helyére, és nyomja le a nyújtófóliát és az üvegszálat, és rögzítse az állórész rögzítőcsövét. Ezután térjen vissza a satuba, és nyomja meg újra laposan. Miután jól illeszkedik a kádba, a sztreccses fóliával és az üvegszállal beillesztve, akkor üvegszálas kendőt adnak hozzá (közepén egy lyukkal az állórész rögzítőcsöve számára).
Most már készen áll a kötőanyag öntésére, általában epoxi vagy poliészter gyantát használnak. Mielőtt ez megtörténne, fontos a gondos előkészítés, mivel miután elkezdte ezt a folyamatot, nem tud igazán megállni. 3D nyomtatott alaplemezt használtam, amelyet korábban készítettem, 1 "lyukkal a közepén és egy lapos lemezzel körülötte. Egy 16" -os 1 "-os alumínium csövet használtam, hogy az állórészre szerelhető cső átférjen és merőlegesen a lapos lemezre. A zöld formázó kád, az állórész tekercselése és az állórész rögzítőcsöve lecsúszott a lapos lemezre. Az epoxi keverése előtt először 4 darab zsugorfóliát készítettem fel, és óvatosan helyeztem az ötödik darabot a sötétzöld formázó fánk, így a minimális ráncok lennének az arcon az állórész tekercselésével szemben. Az epoxi keverése és az üvegszálas kendőre öntése után óvatosan lefektettem az 1 "-os cső körüli nyújtófóliát, és képző gyűrűt a tetején. Elkészítettem pár régi fékrotort is, amelyek némi súlyt adtak, és szépen leültem a zöld formázó fánkra. Ezt követően fordított edényt tettem a fék rotorok tetejére, és az edény tetejére körülbelül 100 font cuccot halmoztam. Ezt 12 órán át hagytam, és körülbelül 4-6 mm vastag lett.
4. lépés: Tesztelés és érzékelők
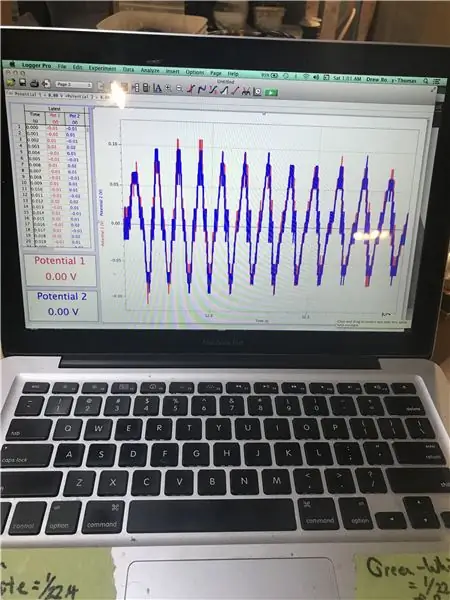
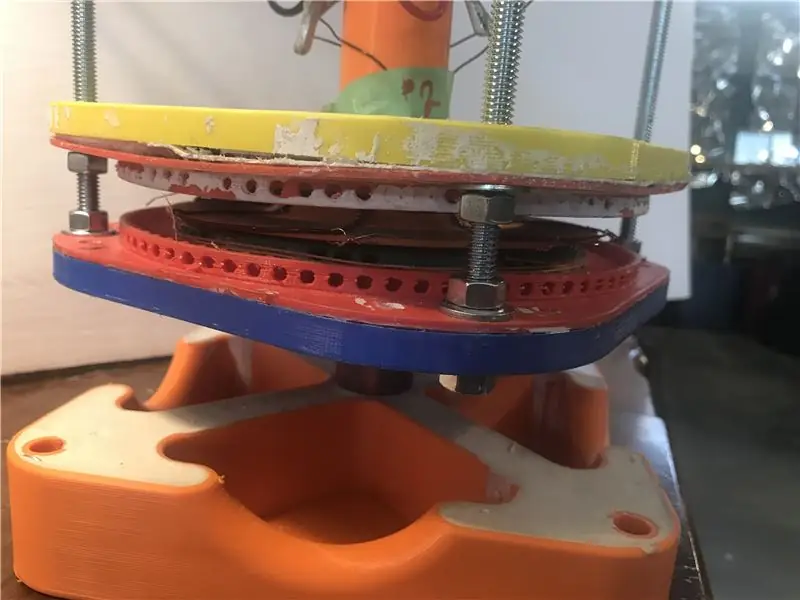
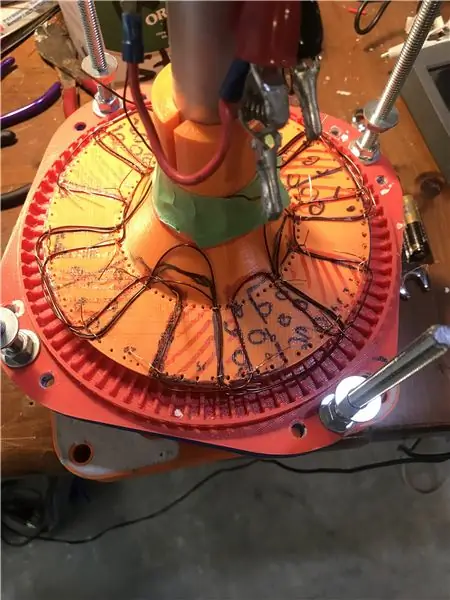
Számos mérhető bemenet és kimenet van a generátorból, és mindezek mérése egyszerre nem könnyű. Nagyon szerencsés vagyok, hogy van néhány olyan eszközöm Vernier -től, amelyek ezt sokkal könnyebbé teszik. Vernier oktatási szintű termékeket gyárt, nem ipari használatra tanúsítvánnyal, de nagyon hasznosak a kísérletezők számára, mint én. Vernier adatgyűjtőt használok, különféle plug and play szenzorokkal. Ebben a projektben csarnok alapú áram- és feszültségszondákat használok a generátor kimenetének mérésére, egy optikai érzékelőt a generátor fordulatszámának megadására, és egy terhelési cellát a nyomaték bemenetének mérésére. Mindezek a műszerek másodpercenként körülbelül 1000 -szer kerülnek mintavételre, és rögzítésre kerülnek a laptopomra, a Vernier naplózót használva AD átjátszó eszközként. A laptopomon a kapcsolódó szoftver valós idejű számításokat futtathat a bemenetek alapján, kombinálva a nyomaték- és fordulatszámadatokat, hogy valós idejű bemeneti tengely teljesítményt adjon meg wattban, és valós idejű kimeneti adatokat elektromos wattban. Még nem fejeztem be ezt a tesztet, és hasznos lenne, ha valaki jobban értene hozzá.
A problémám az, hogy ez a generátor valóban egy mellékprojekt, és ezért nem akarok túl sok időt szánni rá. Úgy gondolom, hogy szabályozható terhelésre használhatom a VAWT kutatásomhoz, de végül szeretnék együtt dolgozni az emberekkel annak finomításán, hogy hatékonyan illeszkedjen a turbinámhoz.
Amikor körülbelül 15 évvel ezelőtt belekezdtem a VAWT -kutatásba, rájöttem, hogy a VAWT -k és más főmozgók tesztelése összetettebb, mint a legtöbb ember gondolja.
Az elsődleges kérdés az, hogy a mozgó folyadék energiája exponenciális a mozgási sebességéhez képest. Ez azt jelenti, hogy amikor megduplázza az áramlás sebességét, az áramlásban lévő energia 8 -szorosára nő (kockára van osztva). Ez problémát jelent, mivel a generátorok lineárisabbak, és általában, ha megduplázza a generátor fordulatszámát, akkor körülbelül 2x wattot kap.
Ez az alapvető eltérés a turbina (energiagyűjtő eszköz) és a generátor (a tengely teljesítménye a hasznos elektromos energia) között megnehezíti a szélturbina generátorának kiválasztását. Ha olyan szélturbinás generátort választ, amely 20 km/órás szélben a legtöbb rendelkezésre álló energiát fogja termelni, akkor valószínűleg nem is kezd el fordulni 20-25 km/óráig, mivel a generátor terhelése túl nagy lesz.. Ezzel a generátor egyezéssel, ha a szél meghaladja a 20 km -t, a turbina nemcsak a nagyobb sebességű szélben rendelkezésre álló energia töredékét fogja fel, a turbina is megfordulhat, és megsérülhet, mivel a generátor által nyújtott terhelés nem nagy elég.
Az elmúlt évtizedben a megoldás gazdaságosabbá vált a vezérlőelektronika árának csökkenése miatt. Ahelyett, hogy megpróbálna megfelelni egy sebességtartománynak, a tervező kiszámítja a készülék maximális működési sebességét, és egy generátort választ az energiamennyiség és a turbina ideális fordulatszáma alapján, vagy valamivel magasabb. Ez a generátor, ha csatlakoztatva van a terheléséhez, általában túl nagy nyomatékot biztosít alacsony fordulatszám -tartományban, és a túlterhelt turbina nem veszi fel az összes energiát, amely akkor lenne, ha megfelelően terhelnék. A megfelelő terhelés létrehozásához egy vezérlőt adnak hozzá, amely pillanatnyilag lekapcsolja a generátort az elektromos terhelésről, lehetővé téve a turbina felgyorsítását a megfelelő sebességre, és a generátort és a terhelést újra csatlakoztatják. Ezt MPPT -nek (Multi Power Point Tracking) hívják. A vezérlő úgy van programozva, hogy a turbina fordulatszámának változásával (vagy a generátor feszültségének emelkedésével) a generátort másodpercenként ezerszer csatlakoztatják vagy lekapcsolják, hogy megfeleljen az adott fordulatszámra vagy feszültségre programozott terhelésnek.
Ajánlott:
3D nyomtatott Twin Paddle Cw kulcs (566 gramm): 21 lépés (képekkel)
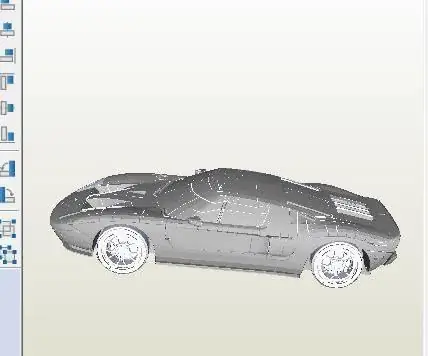
3D nyomtatott Twin Paddle Cw Key (566grs.): Eddig egy pontos, puha és heavy_duty iker kulcs volt, ami sok pénzt költött. Ennek a kulcsnak a tervezésekor az volt a célom, hogy lapátot készítsek: a)- Olcsó --- Műanyagból készült, szabványos 3D nyomtatóval b)- Tartós --- golyót használtam
3D nyomtatott kefe nélküli motor: 7 lépés (képekkel)
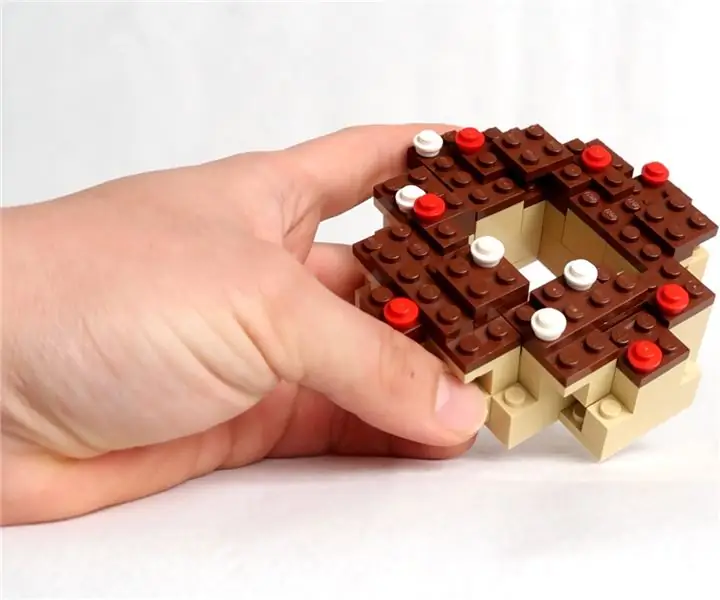
3D nyomtatott kefe nélküli motor: Ezt a motort a Fusion 360 segítségével terveztem a motorok bemutatására, ezért gyors, de koherens motort akartam készíteni. Világosan mutatja a motor alkatrészeit, így modellként használható az ecsetben található alapvető működési elvekre
3D nyomtatott spirométer: 6 lépés (képekkel)
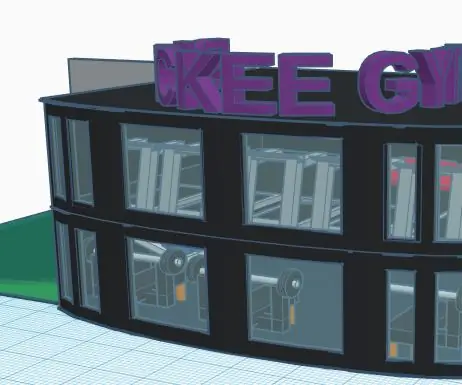
3D nyomtatott spirométer: A spirométerek a klasszikus műszerek a szájból kifújott levegő elemzésére. Ezek egy csőből állnak, amelyet belefújnak, és amely rögzíti egy lélegzetvétel hangerejét és sebességét, amelyet aztán összehasonlítanak a normál értékek alaphalmazával
3D nyomtatott LED hangulatjelző lámpa: 15 lépés (képekkel)
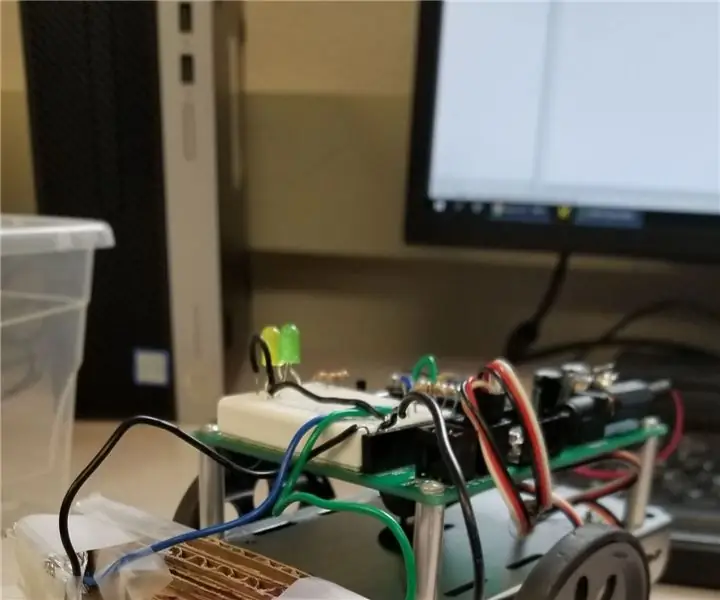
3D nyomtatott LED hangulatjelző lámpa: Mindig is elbűvöltem a lámpákat, így a 3D nyomtatás és az Arduino LED -ekkel való kombinálásának lehetőségemre volt szükségem. A koncepció nagyon egyszerű, és az eredmény az egyik legmegfelelőbb vizuális tapasztalatokat tudsz felmutatni
Egy generátor öngerjesztése egyenáramú generátor, kondenzátor bank vagy akkumulátor nélkül: 5 lépés (képekkel)
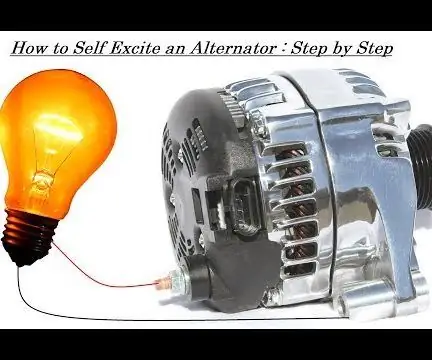
Öngerjesztés generátor, egyenáramú generátor, kondenzátor bank vagy akkumulátor nélkül: Szia! Ez az utasítás arra szolgál, hogy a mezőgerjesztett generátort öngerjesztővé alakítsuk át. Ennek a trükknek az az előnye, hogy nem kell bekapcsolnia a mezőt generátor 12 voltos akkumulátorral, de helyette magától bekapcsol, így